Web Application Service Agreement Directory
Unlock Your Aftermarket Service Potential With a Content Hub.
Let’s talk about how we can help you transform your content, empower your team, and increase online sales revenue.
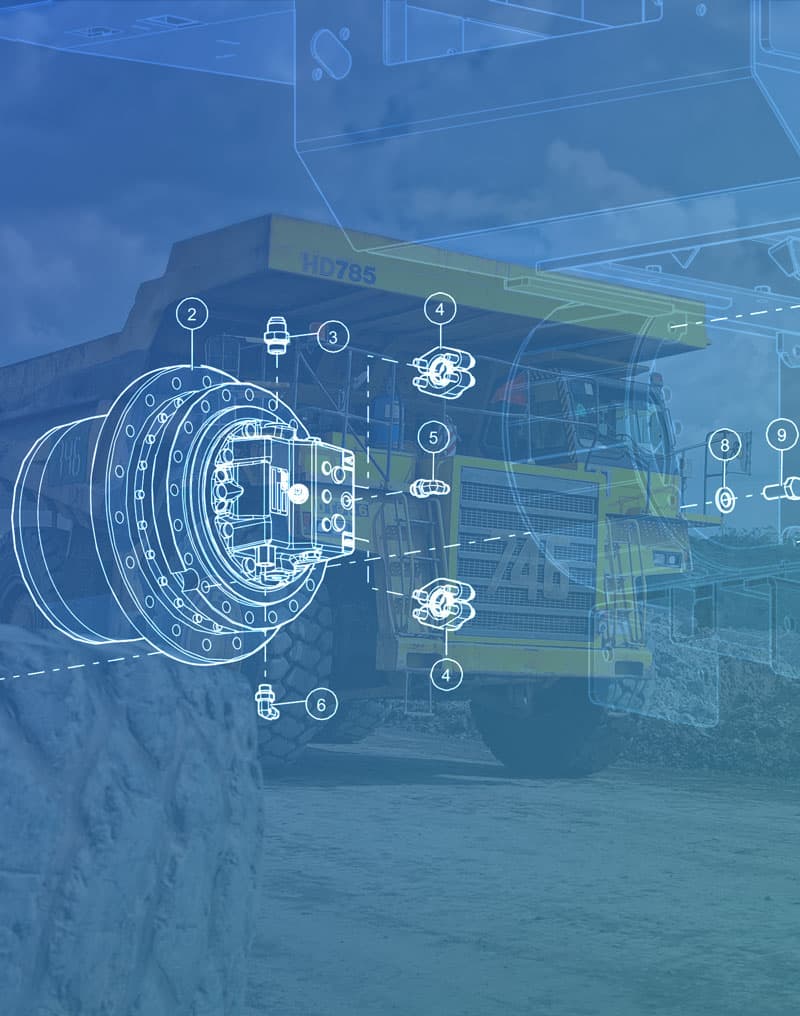
Request A Demo
Complete the form below and we will reach out to coordinate a customized demo.